Introducing the first Sliding Headstock Type CNC Automatic Lathe Cincom L32XII model with an ATC (automatic tool changer)!
- Reducing downtime and contributing to high-variety, low-volume manufacturing -
Citizen Machinery Co., Ltd.
Citizen Machinery Co., Ltd. (Headquarters: Miyota-machi, Kitasaku-gun, Nagano-ken, President: Keiichi Nakajima) will release the Cincom L32XII model with an ATC (automatic tool changer), a sliding headstock type CNC automatic lathe Cincom L32XII model with an ATC which allows automatic replacement of the B axis tool used for various slant machining in April 2021.
The new product will be exhibited at the CITIZEN MACHINERY ONLINE PRIVATE SHOW 2021 starting on February 3, 2021.
ATC is equipped on a machine with a maximum machining diameter of 32 mm (optional 38 mm) for the first time and will be rolled out mainly in Japan as well as North America, as a machine which allows combined and complex machining, reduction in downtime, and high-variety, low-volume production.
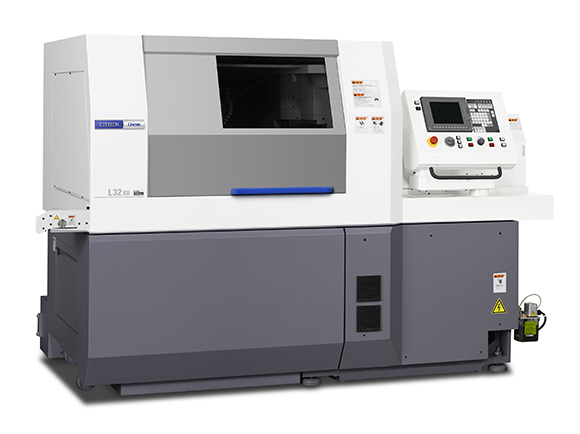
Many of our customers have been looking for a combined machining model with a maximum machining diameter of 32 mm, which would allow more efficient machining of precision machinery parts, such as milling used for the machining of flat and curved surfaces on materials using rotating tools that have previously been done with a machining center. To meet these needs, we have developed an ATC which supports the Cincom L32XII model based on the technology we have cultivated through the Cincom L20XII model with ATC that was launched in 2020.
With the automatic replacement of the B axis tool which performs slant machining, more combined and complex machining will be supported. Furthermore, as the tool is passed on directly from the tool magazine located in the cutting room to the ATC spindle, tool replacement can be done in only four seconds, without stopping the machine.
With ATC, 13 pieces of B axis tools can be set as one setup; therefore, in addition to complex parts machining such as implants and other medical parts, multiple parts can be machined continuously in one setup, reducing the downtime and contributing to high-variety, low-volume manufacturing.
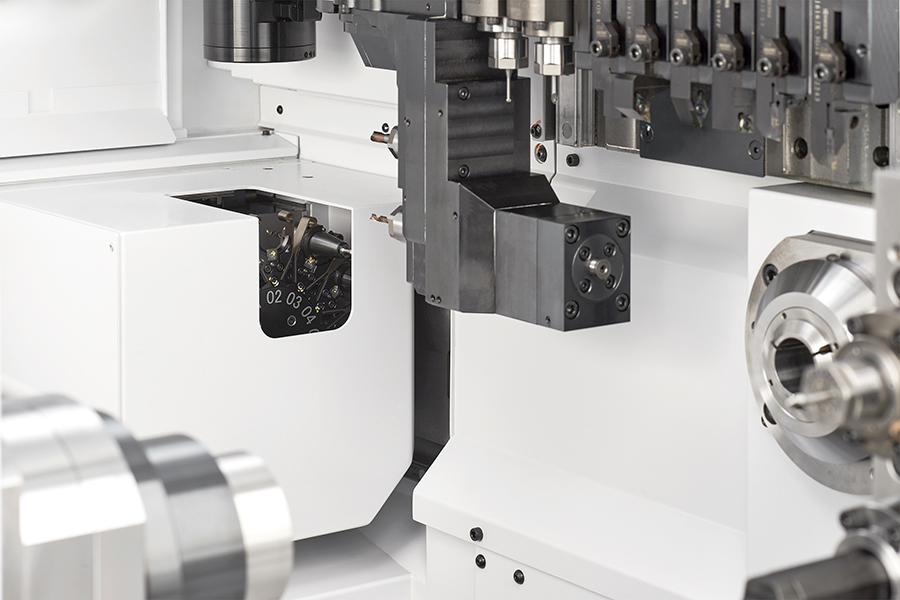
L32 ATC Part
Furthermore, through the optional combined use with LFV (low-frequency vibration cutting) technology (hereafter LFV technology), various issues relating to chips can be solved and further automated, labor-saving operation is made possible.
Specification items
Maximum ATC spindle rotation speed | 12,000min-1 |
Motor output | 2.2KW |
Tool holder type | JBS-15T |
Number of B axis tools | 12 pieces (magazine part) + 1 piece (built in) |
Total number of tools to be mounted on main unit | Max. 34 pieces (including B axis tools) |
Tool replacement duration(chip to chip) | 4.0sec |
Maximum outer diameter of tools | ø30mm |
Maximum grip diameter | ø10mm(ER16) |
Main features of the ATC (automatic tool changer)
1. Combined and complex machining is possible
13 pieces of B axis tools can be set in one setup, enabling a wide variety of machining.
2. Reducing downtime and contributing to high-variety, low-volume manufacturing
As multiple parts can be machined continuously in one setup, this reduces downtime and contributes to high-variety, low-volume manufacturing.
Main machining work
Precision equipment parts, medical instrument parts, electronic equipment parts, automobile-related parts, etc.
Reference: LFV technology
LFV technology is a unique Citizen control technology which breaks up the chips by vibrating the servo axis in the cutting direction and providing “air-cutting” time where the tool does not touch the material. As a result, this achieves solutions to various issues regarding chips, which has been a challenge for many years in the cutting process, such as improvements in the efficiency of small-diameter, deep-hole machining and fine cutting of chips produced when working with difficult-to-cut materials where the resulting chips have tended to be quite long. In addition, this technology achieves machining with high precision for an extended period of time by dramatically reducing the chip volume and preventing defects on the workpiece surface.
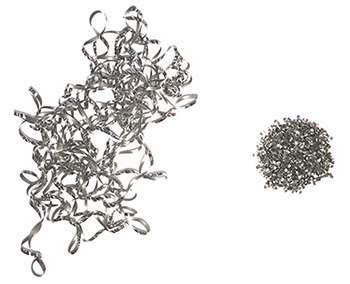
Differences in the shape of chips with the same weight
(material: SUS304)
Left: chips from conventional cutting
Right: chips from LFV technology
- ※
- LFV is a registered trademark of Citizen Watch Co., Ltd.
Reference material: Cincom L32
The sliding headstock type CNC automatic lathe Cincom L32 is the best-selling model with the latest modular design which enables various combinations of optimal features based on your machining needs.
Main Features of L32
1. Achieving the optimal specifications through the introduction of modular design
Function modules which can be combined and a wide range of tooling | ||||
VIII | IX | X | XII | |
B axis (gang rotary tool) | - | 〇 | - | 〇 |
Y2 axis (back tool post Y axis) | - | - | 〇 | 〇 |
Opposite tool post rotary tool | OP | OP | OP | OP |
Back tool post rotary tool | OP | OP | 〇 | 〇 |
2.Flexible support from simple to complex machining
[L32XII model operation axis diagram (with B axis, Y2 axis)] The XII model is equipped with B axis on the gang tool post and Y2 axis on the back tool post.
3. Easy switching between the guide-bushing method and the guide-bushing-less method, reducing running costs
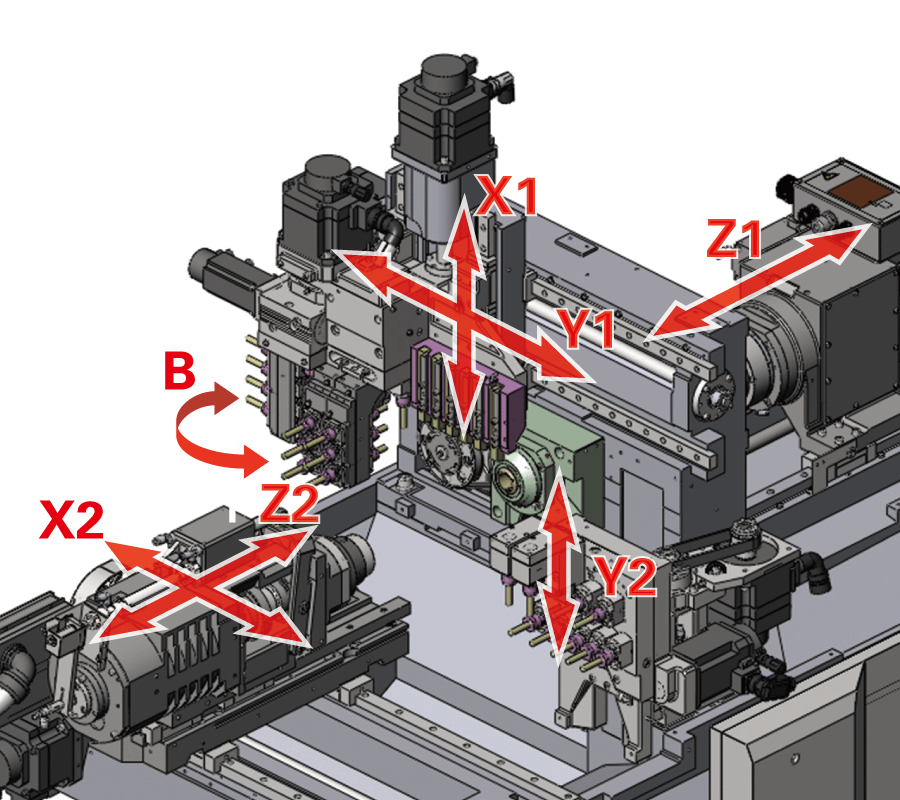
Machine Specifications
Item | L32 VIII | L32 IX | L32 X | L32 XII | |
---|---|---|---|---|---|
Maximum machining diameter | ø32mm | ||||
Maximum machining length | GB machine | 320mm/chuck | |||
GBL machine | Workpiece diameterx2.5/chuck | ||||
Spindle speed | Max.8,000min-1 | ||||
Maximum chuck diameter of back spindle | ø32mm | ||||
Back spindle speed | Max.8,000min-1 | ||||
Rapid feed rate | X1 axis | 32m/min | |||
X2 axis | 32m/min | ||||
Y1 axis | 32m/min | ||||
Y2 axis | - | 24m/min | |||
Z1 axis | 32m/min | ||||
Z2 axis | 32m/min | ||||
Number of tools to be mounted | Max.30 | Max.36 | Max.44 | Max.40 | |
Tool size | Turning tool | □16mm | |||
Motors | For spindle drive | 3.7/7.5kW | |||
For tool spindle drive(gang rotary tool post) | 1.0kW | ||||
For back spindle drive | 2.2/3.7kW | ||||
For spindle drive of opposed tool post | 1.0kW Note) Optional feature to all types | ||||
For spindle drive of back tool post | OP | 1.0kW | |||
Weight | 2,850kg | 2,900kg |
- Maximum machining diamete
- ø32mm
- Maximum machining length [GB machine]
- 320mm/chuck
- Maximum machining length [GBL machine]
- Workpiece diameterx2.5/chuck
- Spindle speed
- Max.8,000min-1
- Maximum chuck diameter of back spindle
- ø32mm
- Back spindle speed
- Max.8,000min-1
- Rapid feed rate [X1 axis]
- 32m/min
- Rapid feed rate [X2 axis]
- 32m/min
- Rapid feed rate [Y1 axis]
- 32m/min
- Rapid feed rate [Y2 axis]
- -
- Rapid feed rate [Z1 axis]
- 32m/min
- Rapid feed rate [Z2 axis]
- 32m/min
- Number of tools to be mounted
- Max.30
- Tool size [Turning tool]
- □16mm
- Motors [For spindle drive]
- 3.7/7.5kW
- Motors [For tool spindle drive(gang rotary tool post)]
- 1.0kW
- Motors [For back spindle drive]
- 2.2/3.7kW
- Motors [For spindle drive of opposed tool post]
- 1.0kW Note) Optional feature to all types
- Motors [For spindle drive of back tool post]
- OP
- Weight
- 2,850kg
- Maximum machining diamete
- ø32mm
- Maximum machining length [GB machine]
- 320mm/chuck
- Maximum machining length [GBL machine]
- Workpiece diameterx2.5/chuck
- Spindle speed
- Max.8,000min-1
- Maximum chuck diameter of back spindle
- ø32mm
- Back spindle speed
- Max.8,000min-1
- Rapid feed rate [X1 axis]
- 32m/min
- Rapid feed rate [X2 axis]
- 32m/min
- Rapid feed rate [Y1 axis]
- 32m/min
- Rapid feed rate [Y2 axis]
- -
- Rapid feed rate [Z1 axis]
- 32m/min
- Rapid feed rate [Z2 axis]
- 32m/min
- Number of tools to be mounted
- Max.36
- Tool size [Turning tool]
- □16mm
- Motors [For spindle drive]
- 3.7/7.5kW
- Motors [For tool spindle drive(gang rotary tool post)]
- 1.0kW
- Motors [For back spindle drive]
- 2.2/3.7kW
- Motors [For spindle drive of opposed tool post]
- 1.0kW Note) Optional feature to all types
- Motors [For spindle drive of back tool post]
- OP
- Weight
- 2,850kg
- Maximum machining diamete
- ø32mm
- Maximum machining length [GB machine]
- 320mm/chuck
- Maximum machining length [GBL machine]
- Workpiece diameterx2.5/chuck
- Spindle speed
- Max.8,000min-1
- Maximum chuck diameter of back spindle
- ø32mm
- Back spindle speed
- Max.8,000min-1
- Rapid feed rate [X1 axis]
- 32m/min
- Rapid feed rate [X2 axis]
- 32m/min
- Rapid feed rate [Y1 axis]
- 32m/min
- Rapid feed rate [Y2 axis]
- 24m/min
- Rapid feed rate [Z1 axis]
- 32m/min
- Rapid feed rate [Z2 axis]
- 32m/min
- Number of tools to be mounted
- Max.44
- Tool size [Turning tool]
- □16mm
- Motors [For spindle drive]
- 3.7/7.5kW
- Motors [For tool spindle drive(gang rotary tool post)]
- 1.0kW
- Motors [For back spindle drive]
- 2.2/3.7kW
- Motors [For spindle drive of opposed tool post]
- 1.0kW Note) Optional feature to all types
- Motors [For spindle drive of back tool post]
- 1.0kW
- Weight
- 2,900kg
- Maximum machining diamete
- ø32mm
- Maximum machining length [GB machine]
- 320mm/chuck
- Maximum machining length [GBL machine]
- Workpiece diameterx2.5/chuck
- Spindle speed
- Max.8,000min-1
- Maximum chuck diameter of back spindle
- ø32mm
- Back spindle speed
- Max.8,000min-1
- Rapid feed rate [X1 axis]
- 32m/min
- Rapid feed rate [X2 axis]
- 32m/min
- Rapid feed rate [Y1 axis]
- 32m/min
- Rapid feed rate [Y2 axis]
- 24m/min
- Rapid feed rate [Z1 axis]
- 32m/min
- Rapid feed rate [Z2 axis]
- 32m/min
- Number of tools to be mounted
- Max.40
- Tool size [Turning tool]
- □16mm
- Motors [For spindle drive]
- 3.7/7.5kW
- Motors [For tool spindle drive(gang rotary tool post)]
- 1.0kW
- Motors [For back spindle drive]
- 2.2/3.7kW
- Motors [For spindle drive of opposed tool post]
- 1.0kW Note) Optional feature to all types
- Motors [For spindle drive of back tool post]
- 1.0kW
- Weight
- 2,900kg